Sustainability stories
Packaging and waste streams at the Lely Campus
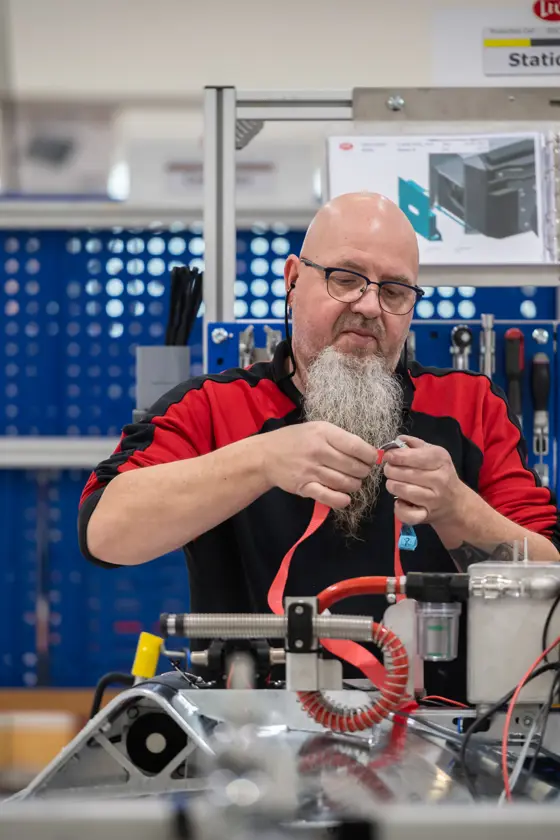
Packaging and waste streams at the Lely Campus
Lely strives towards circular dairy farming. The same ambition is in place for our own products and services. To set a good example we are raising the bar in sustainability: a program has been started in which Lely commits to be carbon neutral in its own operations by 2030. We bundled initiatives from different departments and expertise to create a series called Sustainability Stories. With these stories we showcase our sustainable and circular projects. In this story we highlight the packaging process and waste streams of our production facility at the Lely Campus.
We spoke with Vivian Draaisma, Manufacturing Systems & Processes Engineer at Lely. She works within the Manufacturing Engineering team, location Maassluis.
Reusable systems
An important way to enhance the sustainability of our operational activities is to reduce the amount of non-reusable packaging. We are constantly looking for ways to achieve this for incoming materials. We try to use reusable packaging whenever possible to help maintain the quality of materials during transport and to help increase the efficiency in material handling. Reusable packaging comes in different shapes and forms, for example aluminum racks. The racks are designed by one of the manufacturing engineers, are produced in our own facility and are mostly used for heavy or odd-sized product parts. Product parts do not have to be individually packed and transported, which saves time, space, packaging material and additional handling. Next to the racks, we also work with storage bins (LTB) that are used by our suppliers as a packaging method. Some bins are also accommodated with a foam inlay to ensure the protection of the product. Bins are mostly used for smaller sized parts, for example metal brackets and plates. By providing our racks and bins, we minimize our waste streams and handling activities. We hope to add more products to these reusable systems in the future.”
Quality improvement
We are currently setting up sustainability KPI’s for Operations to improve the way we measure and steer on sustainability aspects, such as the reduction of packaging and our waste streams. That does not mean sustainability is not already intertwined with our current KPI’s. Our KPI for quality is a good example and is one of our five main KPI’s. The department of Quality Assurance & Quality Control and our multidisciplinary teams (OPS teams) have focused on improving our incoming and outgoing quality in the past few years. For example, a system to measure the quality at the end of our assembly lines has been set up. This way it is easier to find what issues we have and solve them more quickly and sustainably. An improved quality on incoming goods means a lower rejection rate and therefore less waste. An improved quality on outgoing robots could lead to a longer lifespan of our products. Both contribute to Lely’s sustainability mission and goals.